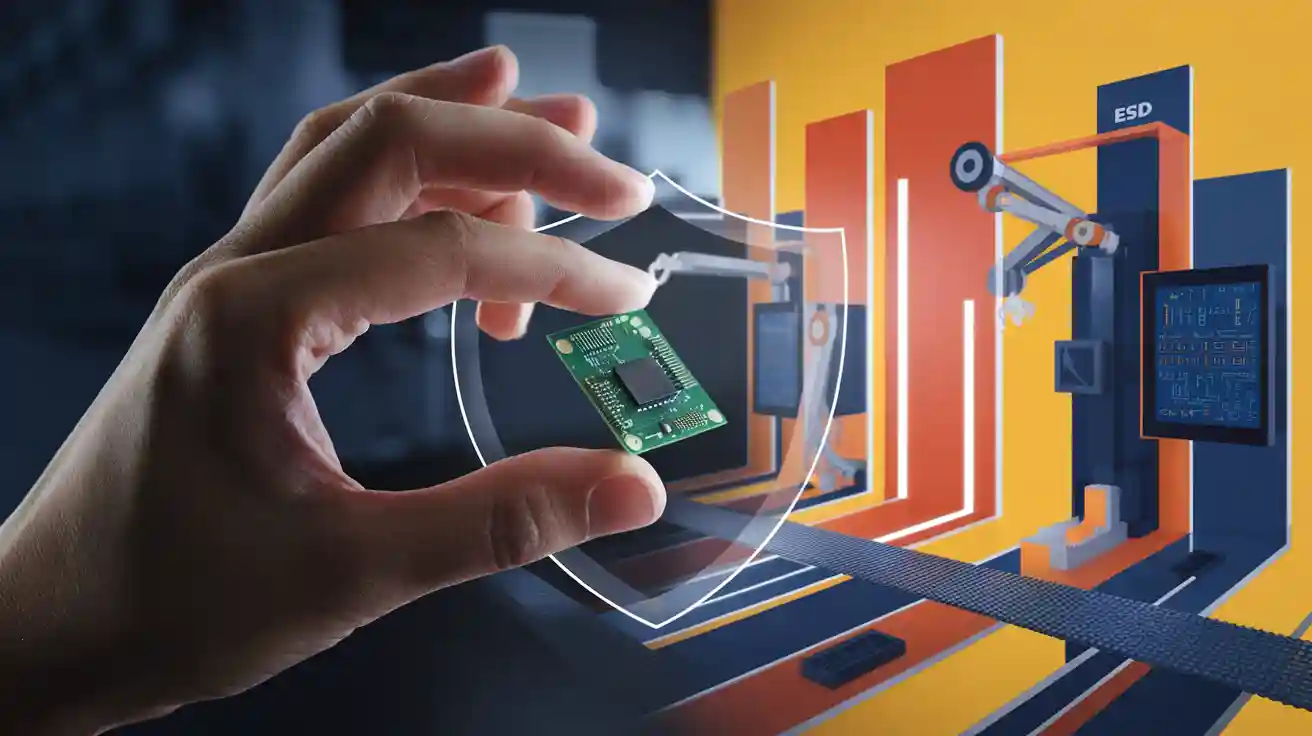
LINK-PP’s smart factory transforms ESD Protection into a seamless process for electronics manufacturers. Reliable network components depend on robust safeguards against electrostatic discharge. LINK-PP leads the industry by embedding advanced ESD solutions directly into Optical Transceivers, RJ45 Connectors, LAN Transformers, and Fiber Optic Cages. This integrated approach enhances product longevity and ensures consistent performance in demanding environments.
Key Takeaways
Electrostatic discharge (ESD) can damage sensitive electronic parts and cause costly failures, making strong ESD protection essential for reliable network components.
LINK-PP’s smart factory uses automation, real-time monitoring, and strict quality controls to keep static levels low and ensure consistent ESD protection during production.
Following industry standards and using factory control methods like static-control flooring and staff training reduce ESD risks and support compliance.
Customers benefit from fewer product failures, easier regulatory compliance, and faster, more reliable sourcing thanks to LINK-PP’s advanced ESD solutions.
Why ESD Protection Matters
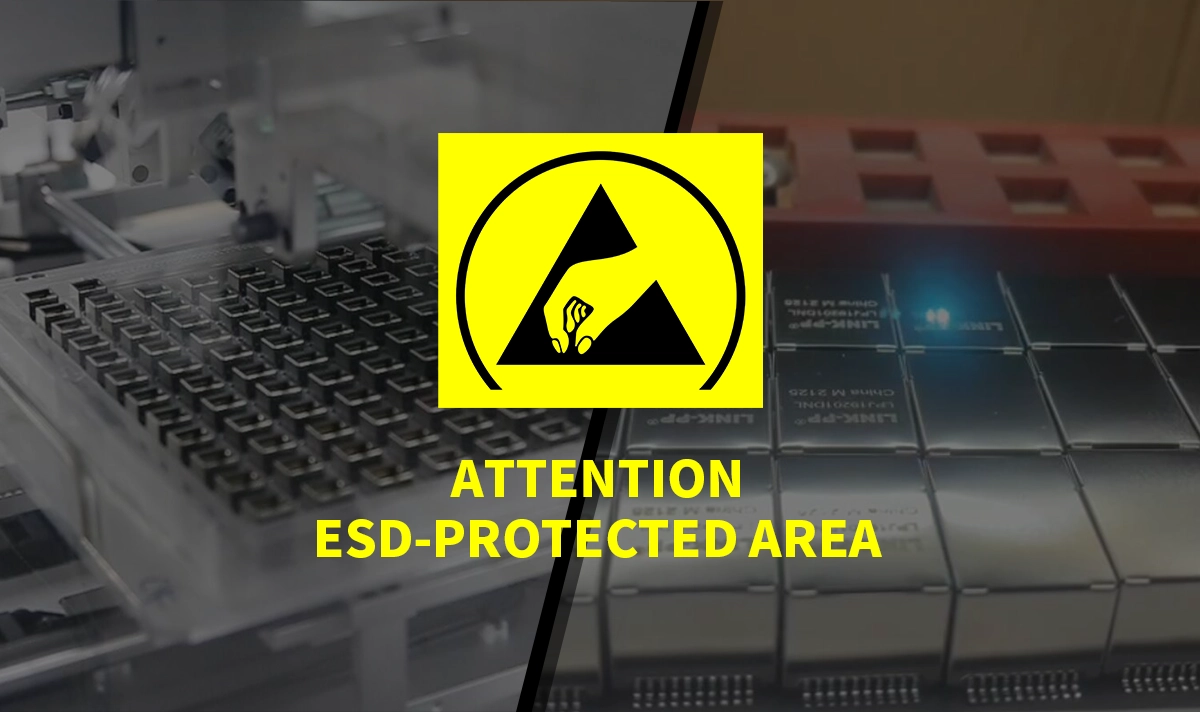
Risks for Sensitive Components
Electrostatic discharge poses a serious threat to modern electronic components. Many devices, such as microprocessors, memory chips, and laser diodes, can suffer damage from voltages as low as 100 volts—or even less. As circuits become smaller and more complex, their sensitivity to ESD increases. Even a single discharge can destroy a component or cause hidden defects that lead to failure later.
Note: The cost of ESD damage rises dramatically depending on where the failure occurs. A simple diode may cost only a few cents to replace, but if the same failure happens on a board or within a system, the cost can reach thousands of dollars. The electronics industry loses billions each year due to ESD-related failures.
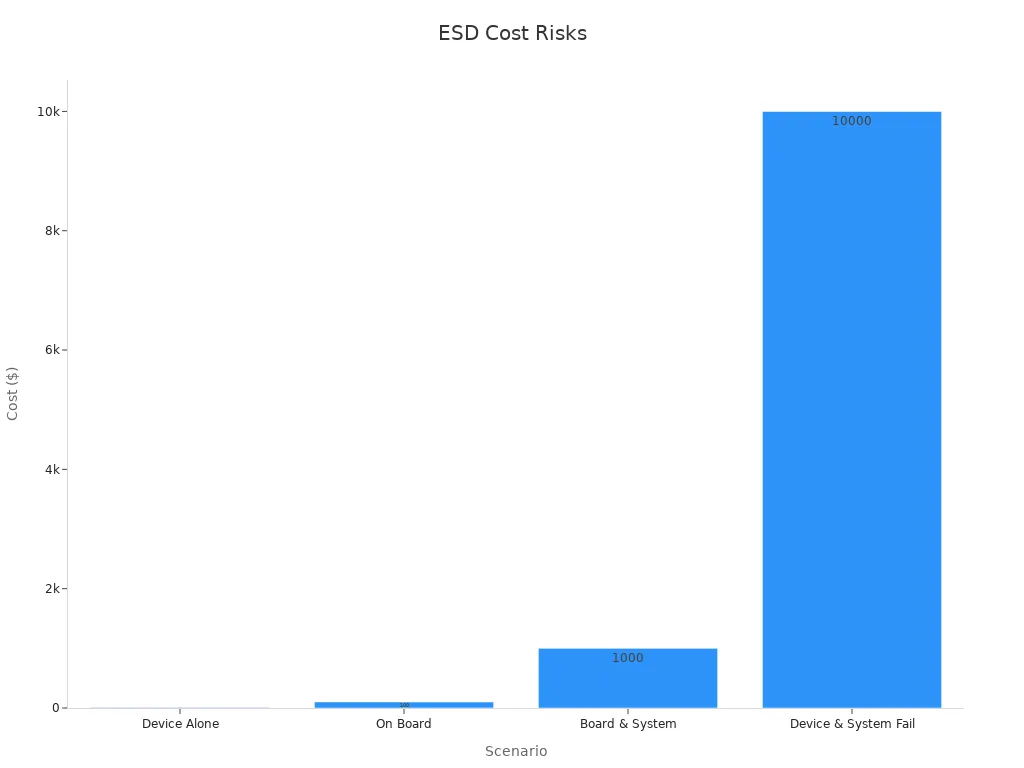
Impact on Network Reliability
ESD events can disrupt network performance and reliability in several ways:
ESD causes high peak currents and rapid voltage drops, which can break down integrated circuits.
Charged Device Model (CDM) events are a leading cause of failures in modern electronics, often occurring in less than a nanosecond.
Advanced chip designs increase vulnerability due to complex electrical interactions.
Full-chip ESD simulation tools help engineers identify weak points and improve protection.
Approximately 20-40% of integrated circuit failures result from ESD events. These failures can cause temporary malfunctions, such as resets or display flickers, and even permanent damage to input/output ports at higher voltages. ESD Protection plays a critical role in preventing these issues, supporting stable network operation and reducing costly downtime.
ESD Risks for LINK‑PP Products
Optical Transceivers & SFP/QSFP Cages
Laser diodes and photodiodes are easily damaged by ESD. Mistouching connector pins—during assembly or quality inspection—can ruin a module.RJ45 Connectors with Magnetics
These include sensitive components like transformers and integrated LEDs. A discharge during soldering or handling may degrade performance.LAN Transformers
With critical isolation layers, transformers must be carefully protected from static-induced insulation breakdown.
ESD Protection Strategies
Industry Standards
Industry standards set the foundation for effective ESD control in electronics manufacturing. These benchmarks guide companies in designing safe environments and reliable products. The following table highlights key standards that shape global ESD Protection practices:
Standard | Scope/Application | Description |
---|---|---|
ANSI/ESD S20.20 | United States, General Industry | Comprehensive framework for ESD control programs covering personnel grounding, packaging, and more. Widely adopted as the gold standard in the US. |
IEC 61340 | International | Harmonizes with ANSI/ESD S20.20, providing guidelines for global markets to ensure product quality and facilitate international trade. |
MIL-STD-1686 | Military and Aerospace | U.S. military standard addressing ESD protection in mission-critical environments with stringent requirements for extreme conditions. |
Additional technical reports, such as ESD TR23.0-01 and ESD TR53-01, offer guidance on control, monitoring, and compliance verification for ESD protective equipment and materials.
Factory Control Methods
LINK‑PP’s Professional ESD Protection Ecosystem
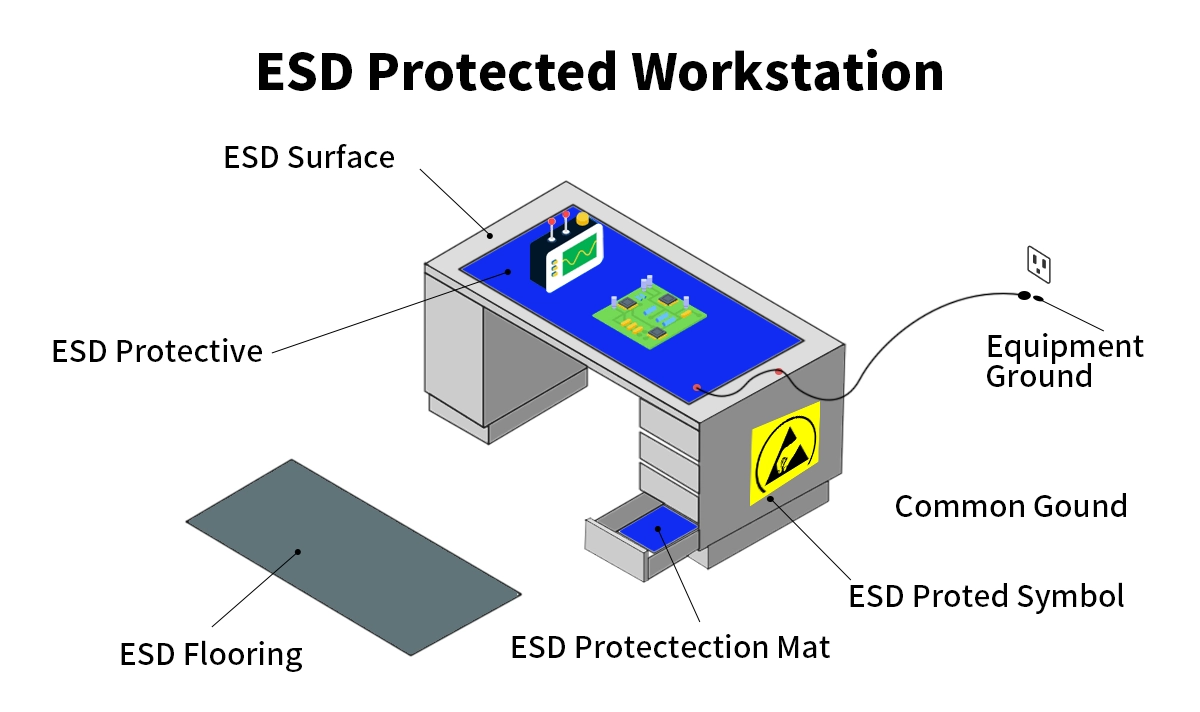
Our manufacturing and R&D facility implements a comprehensive ESD-controlled area (EPA), consistent with IEC 61340‑5‑1 standards:
ESD Workstations equipped with grounded mats and wrist straps to stabilize operator potential.
Antistatic Packaging for storage and transport—each optical transceiver is sealed in an antistatic bag and equipped with a dust cover.
Controlled Environment with stable humidity to reduce static buildup.
Hardware Design for Protection
TVS Diodes & ESD Arrays
Critical signal lines—like Ethernet lanes—are protected using low-capacitance TVS diodes, shielding them from surges up to IEC 61000‑4‑2 levels.Transformer Isolation
RJ45 magnetics provide natural ESD buffering. When paired with PHY-side TVS protection, this offers robust surge defense.PCB Layout Practices
Ground planes, guard traces, and proper isolation ensure any stray electrostatic is safely directed away from sensitive components.
Safe Handling & Assembly Procedures
Our SOPs include essential steps:
Use of Wrist Straps & Grounded Tools when mounting connectors, transformers, or optical modules—aligned with Cisco/Juniper guidelines.
ESD-Safe Storage Materials, like conductive foam and storage bins.
Regular Compliance Audits ensure all materials, operators, and processes meet ESD safety requirements.
Quality Assurance & Final Testing
All LINK‑PP products—including RJ45 connectors with magnetics, LAN transformers, optical transceivers, and fiber optic cages—undergo:
Voltage Withstand Tests, simulating ESD events to confirm insulation and protection.
Eye-Diagram & Signal Integrity Tests to verify full functionality post-manufacture.
Lifecycle & Reliability Tests under thermal, mechanical, and ESD stress conditions.
FAQ
What is ESD and why does it matter in electronics manufacturing?
Electrostatic discharge (ESD) is a sudden flow of electricity between two objects. ESD can damage sensitive electronic parts. LINK-PP’s smart factory uses advanced controls to prevent ESD, which helps protect network components and ensures long-term reliability.
How does LINK-PP ensure ESD protection during production?
LINK-PP uses automated assembly lines, real-time static monitoring, and strict quality checks. These measures keep static levels low and protect sensitive devices. The smart factory approach reduces human error and maintains consistent ESD protection across all products.
Which LINK-PP products include built-in ESD protection?
LINK-PP integrates ESD protection into transceivers, RJ45 connectors, transformers, and SFP+ cages.
Customers receive components designed for high reliability and safe operation in demanding environments.
Do LINK-PP’s ESD measures help with industry compliance?
Yes. LINK-PP’s processes align with ANSI/ESD S20.20 and IEC 61340 standards. Customers find it easier to pass audits and maintain certifications when using LINK-PP’s ESD-safe products.
Can LINK-PP’s ESD solutions reduce product failures?
LINK-PP’s advanced ESD controls lower dropout rates and minimize failures. Customers report fewer warranty claims and less downtime. Reliable ESD protection leads to better performance and higher satisfaction.