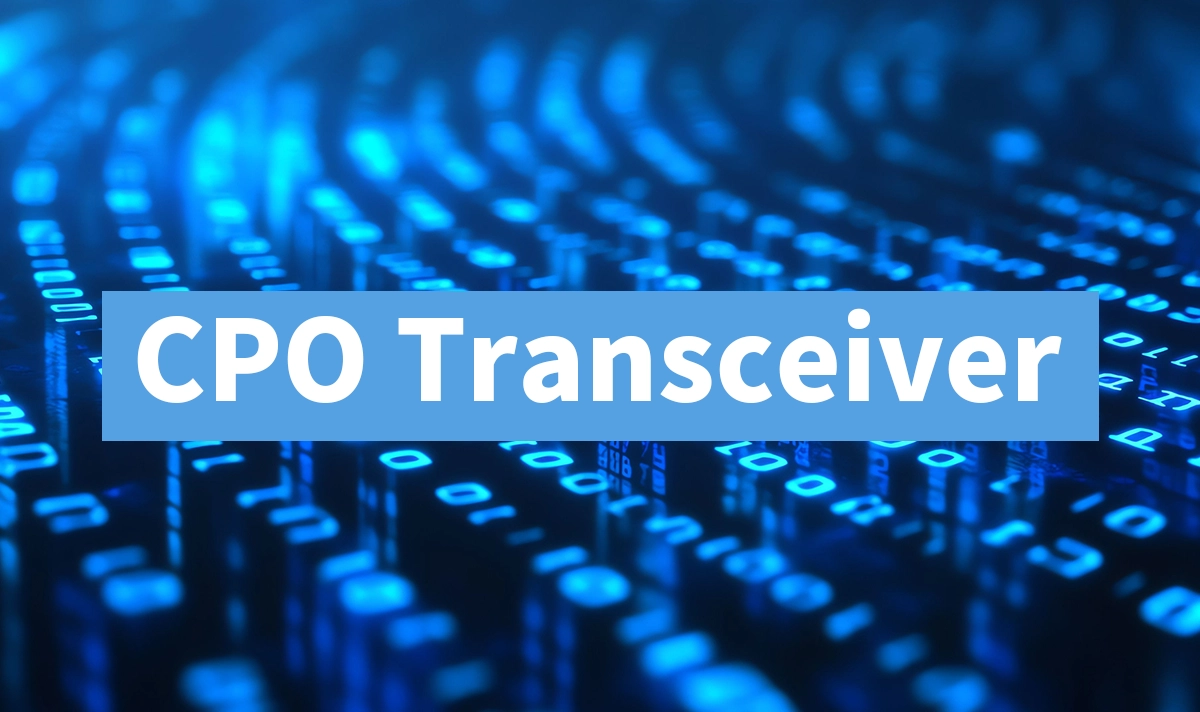
The relentless surge of artificial intelligence, hyperscale computing, and next-generation networks is exposing the limitations of traditional pluggable optical transceivers. Electrical signal integrity challenges, escalating power consumption, and physical density constraints at speeds exceeding 200G per lane demand a fundamental shift. Enter Co-Packaged Optics (CPO), a transformative architecture where the optical engine moves inside the switch ASIC package. This article provides a comprehensive overview of CPO optical modules, exploring their technology, benefits, challenges, and the pivotal role they play in future data centers and AI infrastructure.
➤ Key Takeaways
CPO optical modules put optical and electronic parts together. This helps data move faster and saves power. They make the signal path much shorter, from centimeters to millimeters. This can cut power use by up to half. It also makes latency lower. CPO technology lets more data fit in a small space. This helps data centers handle more data. There are some problems, like heat and hard manufacturing. But better cooling and packaging are helping fix these problems. Data centers, cloud providers, and HPC companies use CPO. They get faster speeds, lower energy costs, and can grow more easily.
➤ Understanding CPO Optical Modules: The Core Innovation
Unlike a conventional pluggable optical transceiver that slots into a front panel, a CPO optical module (often called an optical engine) is integrated directly onto the same substrate or interposer as the switching/routing ASIC. This co-packaging dramatically shortens the high-speed electrical lanes connecting the silicon to the optics.
Key Distinction: The CPO optical transceiver isn't a discrete, hot-swappable unit. It's a tightly integrated assembly of photonic components (lasers, modulators, photodetectors, drivers, TIAs) designed specifically for co-location with the ASIC.
Core Technology Enablers: Silicon Photonics (SiPh), advanced packaging (2.5D/3D integration), and high-density substrates (silicon interposers, organic packages) are critical for realizing functional CPO optical modules.
➤ Why CPO Optical Modules? The Driving Imperatives
The Power Wall Crumbles: Driving high-speed electrical signals (224G PAM4 and beyond) across inches of PCB to reach front-panel pluggables consumes excessive power (~10-15 pJ/bit or more). CPO optical modules reduce this distance to millimeters, potentially cutting I/O power by >50% per bit.
Bandwidth Density Explosion: AI/ML clusters require unprecedented interconnect density. CPO enables packing thousands of optical channels directly beside the ASIC, bypassing front-panel physical constraints and enabling switch capacities exceeding 25.6T and rapidly approaching 51.2T and 102.4T.
Signal Integrity at Extreme Speeds: Shorter electrical paths minimize signal loss, distortion (jitter), and crosstalk, making 224G and future 448G PAM4 per lane feasible and reliable. This is crucial for high-speed optical transceiver performance.
Total System Cost & Efficiency: While initial CPO module costs are high, system-level savings from reduced power consumption, cooling requirements, and potentially simpler PCB designs offer compelling TCO, especially at hyperscale.
➤ Anatomy of a CPO Optical Module: Key Components & Integration
A CPO optical transceiver typically comprises:
Photonic Integrated Circuit (PIC): Usually SiPh-based, integrating modulators (e.g., Mach-Zehnder Modulators - MZMs), photodetectors (PDs), waveguides, and potentially multiplexers/demultiplexers (Mux/Demux). This is the core light manipulation engine.
Electronic Integrated Circuit (EIC): Contains the high-speed electrical drivers for the modulators and transimpedance amplifiers (TIAs) for the photodetectors. Must be located extremely close to the PIC.
Light Source: Typically an external Continuous Wave (CW) laser array. Integrating efficient, high-power lasers directly remains a significant challenge. Light is delivered via fiber or waveguide.
Packaging & Interconnects: Ultra-high-density electrical connections (micro-bumps, hybrid bonding) link the EIC to the ASIC and the EIC to the PIC. Optical coupling (lensed fibers, gratings) connects the PIC to the external fiber array. Advanced thermal management is integral.
➤ CPO Optical Modules vs. Pluggable Transceivers vs. NPO: A Comparative Analysis
Feature | Pluggable Optical Transceiver (e.g., QSFP-DD, OSFP) | Near-Packaged Optics (NPO) Module | Co-Packaged Optics (CPO) Optical Module |
---|---|---|---|
Location | Switch/Router Front Panel | Separate substrate/carrier very close to ASIC | Same substrate/interposer as ASIC |
Electrical Path Length | Long (10-15cm+) | Short (1-5cm) | Ultra-Short (< 1cm) |
Power Efficiency (I/O) | Lower | Moderate Improvement | Highest (50%+ reduction possible) |
Bandwidth Density | Limited by faceplate | Significantly Higher than Pluggable | Highest Potential |
Thermal Management | Per-module | Requires coordination with ASIC cooling | Highly Complex, ASIC + Optics Combined |
Upgradability/Serviceability | Easy (Hot-swap) | Challenging (Often requires system downtime) | Very Difficult (ASIC replacement needed) |
Optical Port Access | Front Panel | Typically edge of board/carrier near ASIC | Internal to ASIC package |
Ecosystem Maturity | Highly Mature | Emerging | Early Development |
Primary Use Case Focus | General Purpose, Flexibility | High-density aggregation, early AI adoption | Ultra-high density, power-critical AI/ML, TOR |
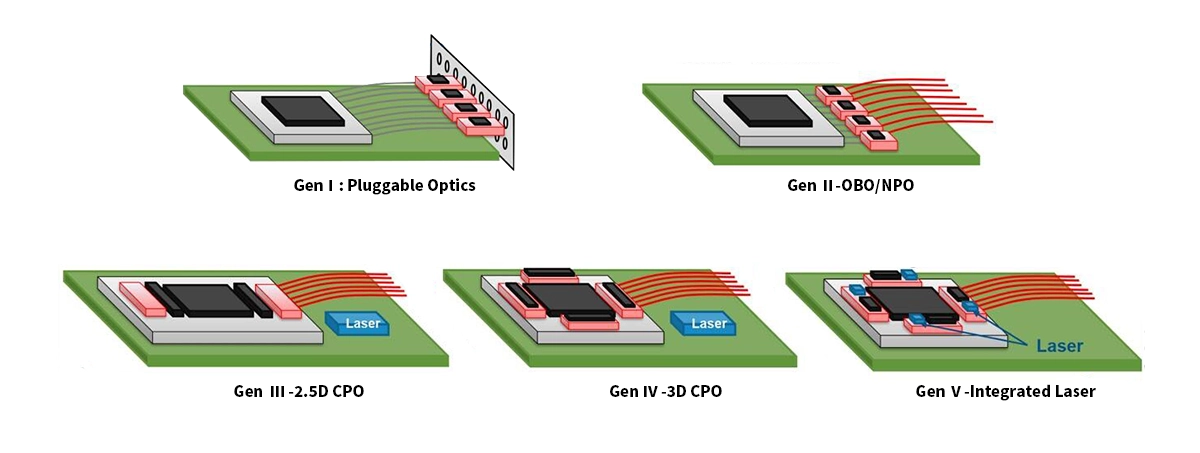
➤ Critical Challenges for CPO Optical Module Deployment
Despite the promise, significant hurdles remain:
Thermal Management: Integrating high-power ASICs (often >700W) with sensitive laser sources and photonics creates intense hot spots. LINK-PP leverages its expertise in thermal solutions – like the copper-core technology used in our 800G SR8 pluggable module – to inform designs for CPO optical transceiver integration, emphasizing efficient heat extraction pathways.
Testability, Yield, and KGD: Testing the optical engine before final ASIC integration is complex and costly. Ensuring Known Good Die (KGD) for both the ASIC and the CPO module is critical for yield. LINK-PP's rigorous optical transceiver testing methodologies developed for products like the LQD-CW400-DR4C are foundational for CPO quality assurance.
Laser Integration: Efficiently coupling light from reliable, high-power lasers into the PIC remains a major technical and cost challenge. External laser arrays (ELAs) are the current solution, but co-packaging or on-chip lasers are desired long-term goals.
Packaging Complexity & Cost: Advanced 2.5D/3D packaging and ultra-precise optical alignment drive up initial costs compared to pluggables. Standardization (e.g., OIF, COBO, OpenEye MSA) is crucial for cost reduction.
Repairability & Supply Chain: A failure in the CPO optical transceiver component typically necessitates replacing the entire ASIC package, impacting operational costs. The ecosystem for co-packaged components is still nascent.
➤ LINK-PP: Bridging Today's Needs with Tomorrow's CPO Vision
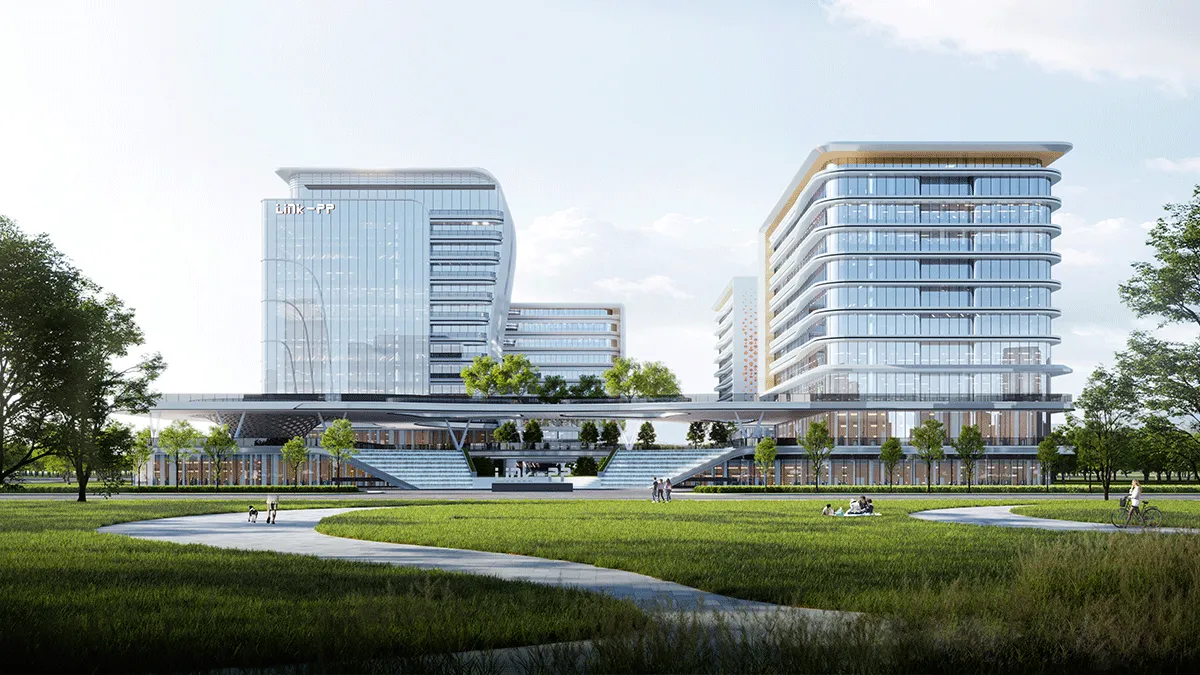
While CPO optical modules represent the future frontier, LINK-PP provides the high-performance, reliable optical transceiver solutions essential for current and transitional infrastructure:
Leading-Edge Pluggables: Our portfolio delivers the density and efficiency demanded by evolving networks. Explore our 800G optical transceiver options like the LQD-M31800-DR8C QSFP-DD for 500m SMF reaches or the LQD-M85800-SR8C for high-bandwidth intra-data center links. For 400G needs, consider the power-optimized LQD-CW400-FR4C QSFP-DD.
NPO-Ready Expertise: LINK-PP is actively developing optical engine technologies and integration knowledge relevant to Near-Package Optics (NPO), the critical stepping stone towards full CPO. Our work on advanced thermal management, evident in modules like the LQ-LW100-ZR4C QSFP28, is directly applicable.
Investing in the CPO Future: LINK-PP is committed to innovation in silicon photonics and co-packaging architectures. We are developing CPO optical transceiver building blocks and participating in industry consortia to drive standards, ensuring our solutions are ready for the co-packaged era. Ask about our CPO optical engine development kits.
➤ Conclusion: The Inevitable Integration
CPO optical modules are not merely an incremental step; they represent a fundamental architectural shift essential for sustaining Moore's Law for bandwidth and overcoming the power limitations plaguing modern data centers. While challenges in thermal management, testability, and initial cost persist, the compelling advantages in power efficiency, bandwidth density, and performance at extreme speeds make CPO inevitable for the most demanding applications. The transition is underway, moving through NPO towards full co-packaged integration.
Ready to Explore the Future of Optical Connectivity?
LINK-PP is your partner for cutting-edge optical solutions, from today's highest-performance pluggables to the co-packaged optics modules of tomorrow.
Optimize Your Current Network: Discover our extensive range of high-speed optical transceivers, including 800G, 400G, and 100G solutions.
Prepare for CPO & NPO: Contact our technical experts to discuss your roadmap for next-generation co-packaged optics integration and learn about LINK-PP's advanced optical engine development.
Access Cutting-Edge Technology: Inquire about our CPO optical transceiver component development and future-ready solutions.
FAQ
What is a CPO optical module?
A CPO optical module puts optical and electronic parts together. This helps data centers send data faster. It also uses less power than old designs.
What benefits does CPO technology provide?
CPO technology gives higher bandwidth and lower power use. It also lowers latency. Data centers can move more data with less energy. This saves money and makes things work better.
What challenges do CPO optical modules face?
CPO modules have problems with heat and are hard to make. The industry needs better rules and more suppliers. This will help more people use CPO modules.
What industries use CPO optical modules?
Data centers, cloud providers, and HPC companies use CPO modules. These groups need fast and efficient data transfer for their work.
What makes CPO modules different from traditional optical modules?
CPO modules put optical engines and switch chips together. Traditional modules keep these parts apart. CPO modules have shorter signal paths. This makes them faster and more efficient.