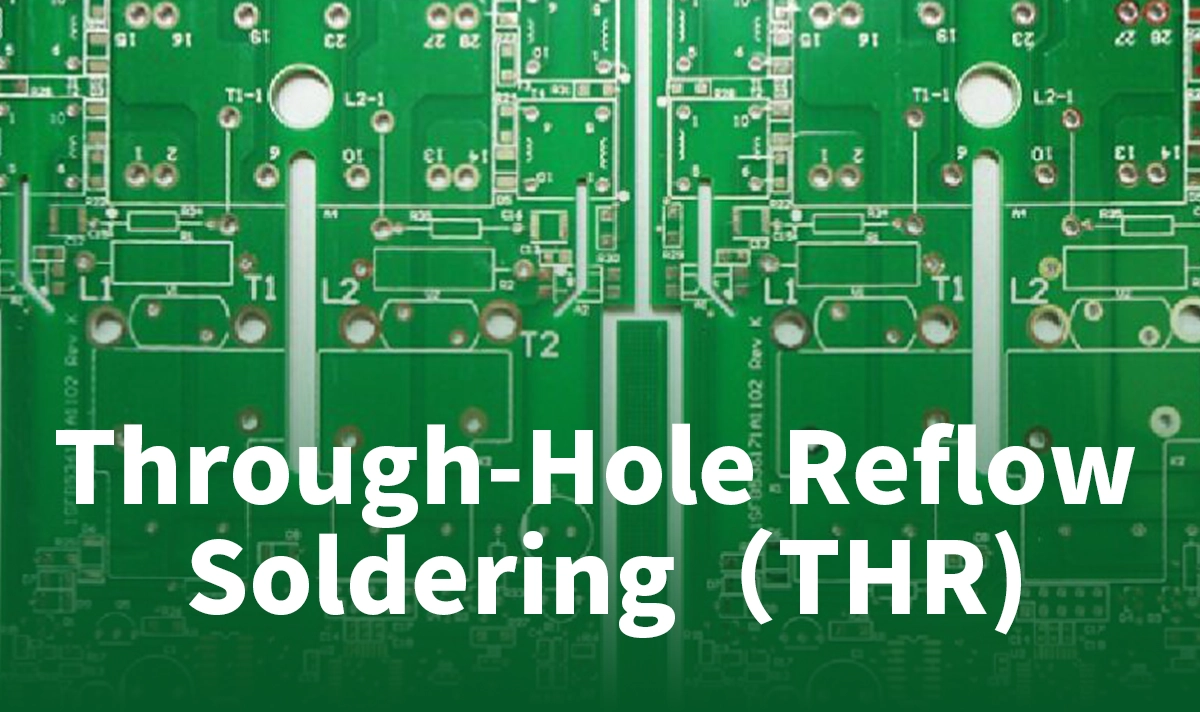
Through‑Hole Reflow Soldering, also called pin-in-paste or intrusive soldering, lets you solder both through-hole and surface-mount parts in one reflow process. Through‑Hole Reflow Soldering (THR) offers exactly this: a hybrid process that marries the durability of Through‑Hole Technology (THT) with the speed and automation of Surface‑Mount Technology (SMT). This method works well with SMT assembly lines. Market reports show that reflow soldering, including through-hole applications, increases efficiency and sees growing use in electronics manufacturing.
Background: Why THR Matters
THT (Through‑Hole Technology) involves placing component leads through PCB holes and soldering from the underside. This method delivers strong mechanical interconnections, ideal for connectors, power components, or high‑stress environments.
SMT (Surface‑Mount Technology) places components on the board surface with solder paste and reflows them in an oven—efficient, precise, and suited for miniaturization.
THR combines both: THT‐style components are equipped to be reflow‐soldered alongside SMT parts, enabling a single, streamlined production flow without wave‑soldering.
THR Process Overview
Through-hole reflow soldering integrates seamlessly into standard SMT production lines. The typical workflow includes the following steps:
Step 1: The PCB is fabricated with plated-through holes (PTH), ensuring proper metallization for soldering.
Step 2: On the SMT line, the board is aligned under a solder paste stencil in preparation for printing.
Steps 3–4: During the solder paste printing stage, the paste is applied across the stencil, filling both the surface-mount pads and partially entering the PTHs.
Steps 5–6: Components are placed using an automated pick-and-place machine. Surface-mount devices (SMDs) are positioned first. If the machine is not capable of placing the through-hole components, they are inserted manually after the SMDs. The leads pass through the holes filled with solder paste, where some paste adheres to the pins, while most remains inside the holes.
Steps 7–8: The board then enters the reflow oven. As the temperature rises, the solder paste melts and flows around the component leads and into the plated hole walls. A reliable solder joint is formed through the creation of an intermetallic compound (IMC) between the component lead, the solder, and the copper plating inside the hole.
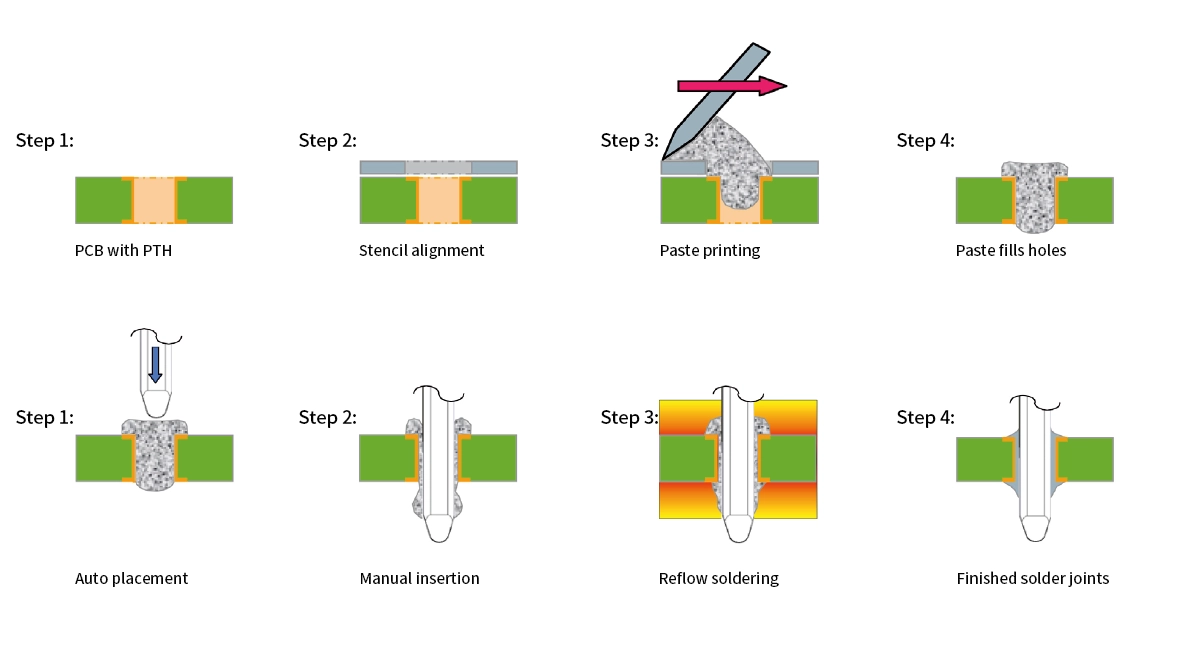
This streamlined process allows both SMD and through-hole components to be soldered in a single reflow cycle, reducing manufacturing steps while ensuring robust mechanical and electrical connections—particularly important for high-reliability parts such as LINK-PP's THR-compatible RJ45 connectors.
Benefits of THR
Mechanical Integrity
Through‑hole leads anchor into the board, securing larger or high‑stress components—like RJ45 connectors—against vibration and handling.One‑Step Assembly
THR eliminates wave soldering, enabling SMT and THR parts to be processed together on the reflow line—saving time, reducing labor, and slashing costs.Scalability
By leveraging automated SMT lines, THR suits both small and large production runs—ideal for EMS providers and mixed-volume OEMs.
Design Considerations & Best Practices
Success with THR depends on thoughtful PCB and component engineering:
Component Requirements
Materials must withstand reflow temperatures (typically up to 260 °C). LINK‑PP’s LPJG0926HENLS4R PoE+ RJ45 connector uses high-temp thermoplastics and leads optimized for THR.
Stand‑Off & Lead Design
A stand‑off from the board allows paste to wick and improve airflow. Pin length must be carefully calibrated—too long, and paste extrusion causes defects; too short, and joints fail IPC‑610 criteria.
Paste Stencil Design
Ensure paste fills appropriately: high‑viscosity paste helps fill holes and prevents voids, as recommended in LINK‑PP’s THR support literature .
Reflow Profile
Use a controlled ramp–soak–peak–cool curve. Ensure paste reaches liquidus, activating flux and avoiding thermal shock to components.
Inspection & Standards
Finalize quality using AOI, x‑ray, and IPC‑610 criteria. THR joints should show ≥75 % solder coverage with <30 % voids.
📦 LINK‑PP’s THR‑Ready Connectors
LINK‑PP designs several THR‑compatible RJ45 connectors—especially the LPJG0926HENLS4R PoE+ RJ45—with:
High-temp housing (PA46 + 30 % glass) enduring 260 °C reflow for 10 s.
1.25 mm stand‑off for airflow and paste flow.
2.40 mm pin length suited to typical 1.6 mm PCBs.
High-viscosity paste compatibility, reducing voids and enhancing joint reliability.
These features ensure LINK‑PP’s THR connectors meet IPC‑610, offering high durability and strong electrical performance in harsh environments.
Typical Applications
Networking & Telecom: High-density RJ45 ports benefit from THR’s mechanical stability plus SMT line speed.
Industrial & Automotive: Vibration resistance and high-current tolerance mesh well with THR’s strengths.
EMS & High‑Volume Production: A single reflow pass boosts throughput and reduces capital expenditure.
THR vs. THT vs. SMT at a Glance
Technology | Assembly Method | Strengths | Limitations |
---|---|---|---|
THT | Leads + wave solder | Extremely robust mechanical joints | Manual labor, no SMT integration |
SMT | Paste + reflow | Compact, fast, automated | Less mechanical durability |
THR | Paste + reflow (hole) | Mechanical + automated efficiency | Requires THR‑rated parts, process tweaks |
Why Choose THR?
THR strikes a compelling balance: it maintains the mechanical resilience of through‑hole mounts while harnessing the rapid, automated reflow process of SMT. For multi‑component PCBs—especially those including heavy connectors like RJ45—THR is the strategic choice.
When you use LINK‑PP’s THR‑optimized RJ45 series, you ensure reliable soldering, consistent quality, and streamlined production workflows—all backed by rigorous design and industry-certified standards.
🏁 Conclusion
Through‑Hole Reflow Soldering (THR) is a forward‑looking hybrid soldering technology that offers the best of both worlds: durable mechanical joints and high‑efficiency SMT assembly. By designing for THR—at the component, PCB, paste, and process level—manufacturers can reduce costs, improve yields, and deliver greater reliability.
At LINK‑PP, THR‑capable components exemplify this philosophy. From material selection to stand‑off geometry and paste compatibility, every detail supports a smoother reflow process and stronger end products. Discover LINK‑PP’s THR solutions—built for performance, designed for scale, and ready for tomorrow’s high‑stress environments.
FAQ
What is the main advantage of Through‑Hole Reflow Soldering?
You can solder both through-hole and surface-mount parts in one process. This method saves time and increases efficiency on your assembly line.
What types of components work best with Through‑Hole Reflow Soldering?
You should use components that can handle high temperatures. Most connectors, switches, and large capacitors work well with this process.
What happens if you use too little solder paste?
You may see weak joints or incomplete hole filling. Always check paste volume to ensure strong, reliable solder connections.
See Also
A Comprehensive Guide To Through-Hole Technology Explained
Exploring Surface-Mount Devices And Their Role In Electronics